Managing Remote Warehouse Workers: Best Practices for Success
Discover best practices for managing remote warehouse workers, from tech solutions to team culture, ensuring efficiency and employee satisfaction.
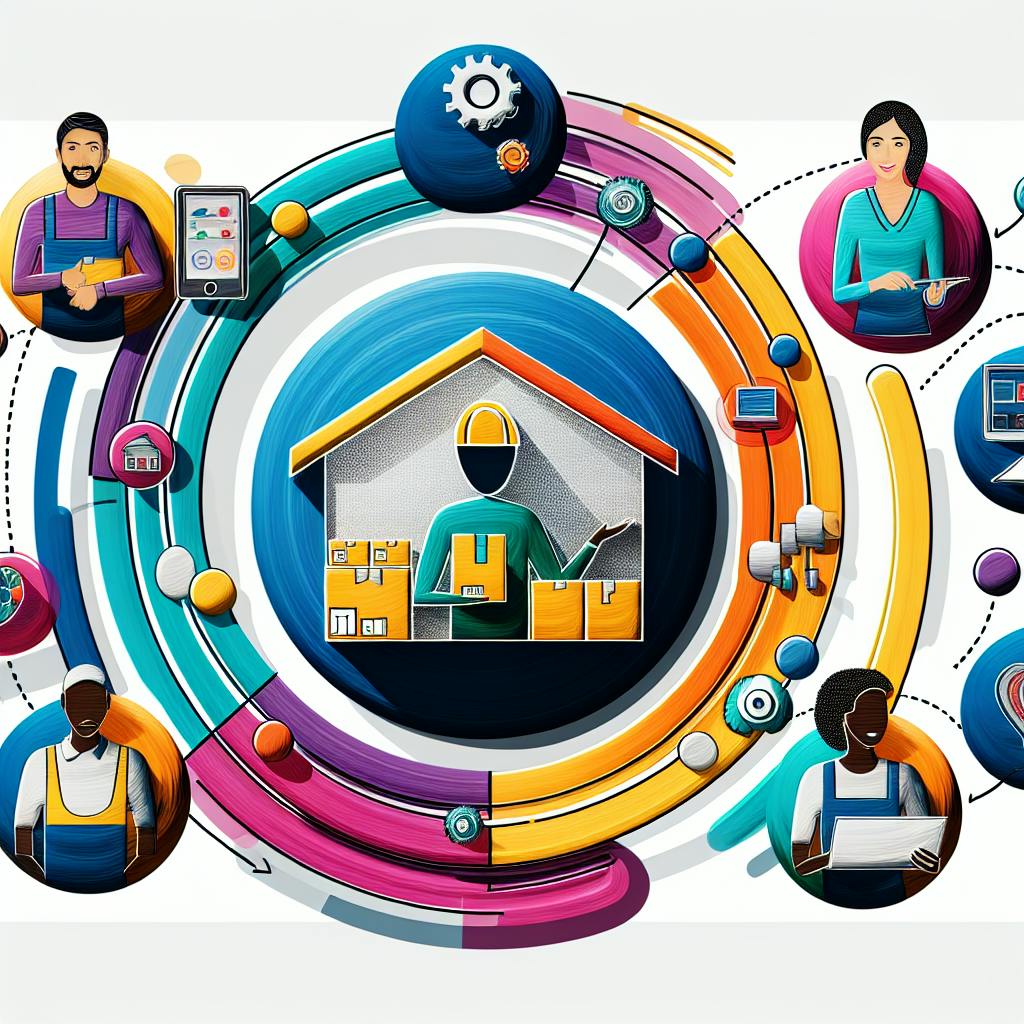
Remote warehouse management is changing the game. Here's what you need to know:
- 74% of workers want remote options, including warehouse staff
- Remote work can lower costs and expand your talent pool
- Key challenges: finding good workers, adopting new tech, and tracking inventory
To succeed with remote warehouse management:
- Use the right tech: WMS, cloud inventory, communication tools
- Set clear goals and track performance
- Build a strong team culture
- Provide ongoing training and support
- Streamline processes for remote work
- Ensure data security and compliance
Aspect | Remote Work | On-Site Work |
---|---|---|
Location | Home or office | Physical warehouse |
Tech Use | Heavily digital | Mix of digital and hands-on |
Visibility | Software data | Direct observation |
Communication | Video calls, chat | Face-to-face and digital |
Cost | Lower overhead | Higher facility expenses |
Scalability | Easier to scale | Limited by physical space |
The future of remote warehouses includes AI forecasting, autonomous robots, and IoT devices. To stay competitive, balance new tech with your team's needs and offer flexible work options.
Related video from YouTube
What is Remote Warehouse Work?
Remote warehouse work is running warehouse operations from afar. It's all about managing inventory, tracking assets, and coordinating logistics without being there in person.
Roles and Tasks
Remote warehouse workers juggle a bunch of responsibilities:
- Keeping tabs on inventory
- Fulfilling orders
- Coordinating shipping
- Monitoring performance
- Optimizing the supply chain
They do all this using fancy software and cloud systems that give them real-time info on inventory, staff productivity, and order status.
Remote vs. On-Site Work
Aspect | Remote Work | On-Site Work |
---|---|---|
Where | Home or office | Physical warehouse |
Tech Use | Heavily digital | Mix of digital and hands-on |
Visibility | Software data | Direct observation |
Communication | Video calls, chat | Face-to-face and digital |
Cost | Lower overhead | Higher facility expenses |
Scalability | Easier to scale | Limited by physical space |
Remote warehouse management gives you flexibility and saves money, but you need solid tech. On-site work lets you see and touch inventory, but it costs more to run.
Take Dollar General, for example. They've got over 135,000 people working across 16 distribution centers. Their remote warehouse jobs start at $20.25 an hour, showing there's a real demand for this kind of work.
And check out HERE Asset Tracking. It's a tool that shows how powerful remote warehouse management can be. Dobrina Laleva from HERE says:
"If you're working from home, you need to be even more efficient. You can't waste time searching for assets with phone calls and emails."
This just goes to show how important it is to have smooth processes when you're managing a warehouse remotely. It's all about keeping things running like clockwork, even when you're miles away.
Key Technologies for Remote Warehouse Management
Remote warehouse management needs top-notch tech. Here's what you can't do without:
Warehouse Management Systems (WMS)
A solid WMS is your remote warehouse's best friend. It handles:
- Shipping and receiving
- Inventory tracking
- Order fulfillment
- Paperwork
Cloud-based WMS? Even better. You get real-time visibility, which is HUGE for remote work. Plus, it plays nice with other systems like ERP and TMS.
"Infor WMS lets me manage products from warehouse to shelf. The 3D warehouse view is cool, and I can use it from anywhere", says one happy user.
Cloud Inventory Tracking
Cloud inventory systems are your eyes in the sky. They offer:
- Real-time updates
- Automated stock counts
- Barcode scanning
Less human error, more time saved. Win-win.
One e-commerce company cut stockouts by 35% using SkuNexus cloud inventory. Real-time data for the win!
Team Communication Tools
Remote teams need to talk. A lot. They use:
- Video calls
- Instant messaging
- Project management apps
Everyone stays in the loop, no matter where they are.
Remote Monitoring and Security
Keeping tabs on your warehouse from afar? Crucial. You'll want:
- IoT sensors for real-time monitoring
- Security cameras
- Automated alerts
Example: IoT tech can watch warehouse temperature and humidity. If things go wonky, staff get an alert. Quick action, problem solved.
Tech | Why It's Great |
---|---|
WMS | One-stop management |
Cloud Inventory | Stock updates in real-time |
Communication Tools | Team stays in sync |
Remote Monitoring | Catch issues early |
Tips for Managing Remote Warehouse Teams
Clear Communication is Key
Set up a solid plan for staying in touch with your remote warehouse team. Daily check-ins or weekly one-on-ones can work wonders. Know when to use video calls, emails, or instant messages.
ShipHero, a warehouse management company, uses a smart system to keep remote and on-site teams in sync. Tyler Anderson from ShipHero puts it this way:
"It's easier to find and solve problems sitting in front of your computer, and we want our warehouse managers on the floor."
Track Performance, Set Goals
Keep an eye on important numbers for your remote warehouse staff:
- How fast orders are filled
- How accurate the inventory is
- How quickly items are picked
Write these down. It helps you spot trends and fix issues fast.
Build a Strong Team Culture
Create trust and responsibility in your team:
- Set up casual chat channels
- Do virtual team-building
- Give shout-outs to top performers
Train and Support Your Team
Have clear training programs ready. Cover the basics:
- Using warehouse management systems
- Safety rules
- Communication tools
Don't forget ongoing IT support to keep things running smooth.
Streamline Your Processes
Make workflows remote-friendly. Use good warehouse software to keep data consistent. Ask your team for feedback and update your processes often.
Keep Data Safe, Follow the Rules
Stay secure and compliant:
- Use secure cloud systems
- Train staff on data protection
- Do regular security checks
sbb-itb-796aeb9
Solving Common Remote Warehouse Problems
Remote warehouses face unique challenges. Let's tackle three big ones:
Working Across Time Zones
Time zones can mess with teamwork. Here's how to fix that:
- Use tools like World Time Buddy to convert times
- Share a team calendar showing when everyone's available
- Switch up meeting times so it's fair for everyone
Spacetime.am plugs into Slack, showing where your team is and when they're working. It's a game-changer for planning meetings and tasks.
Managing Inventory Remotely
Counting stock from far away? Not easy. Try these:
- Get real-time inventory tracking software
- Do regular stock checks
- Use RFID tech for super-accurate tracking
Fun fact: RFID systems are over 95% accurate. That's WAY better than old-school methods at 65%. Less mistakes, more efficiency.
Maintaining Quality
No in-person supervision? No problem:
- Set clear goals and metrics
- Use video calls for quality checks when needed
- Put a solid quality control system in place
Take ShipHero, for example. Their smart system lets warehouse managers spot and fix issues remotely. It keeps quality high and frees up managers for the big-picture stuff.
Using AI and Machine Learning in Remote Warehouses
AI and machine learning are transforming remote warehouse operations. These tools boost decision-making and efficiency in off-site management.
AI for Predicting Inventory Needs
AI helps warehouses nail their stock levels. It crunches past sales data to forecast customer demand.
Amazon's AI system checks:
- Past purchases
- Current cart contents
- Wish list items
- Trending products
This keeps Amazon stocked up and ready for orders.
Walmart's AI considers:
- Economic indicators
- Weather forecasts
- Local events
Result? The right products in each store.
To leverage AI for inventory:
1. Clean up your data. Accurate sales records are key.
2. Start small. Test AI on a few products first.
3. Keep at it. AI improves with more data over time.
Machine Learning for Better Processes
Machine learning speeds up warehouse tasks and cuts errors. It tackles:
- Order picking
- Box packing
- Warehouse logistics
Here's how some big players use it:
Company | Tech | Function |
---|---|---|
Amazon | Sparrow robot | Product handling |
FedEx | Sorting robot | Package routing |
These robots use computer vision to handle items. They work 24/7 with fewer mistakes than humans.
To bring machine learning into your warehouse:
1. Audit your current operations. Spot time-sinks and error-prone tasks.
2. Choose one area to improve. Don't overhaul everything at once.
3. Train your staff. Ensure they can work alongside the new tech.
AI and machine learning are game-changers for remote warehouses. They sharpen inventory predictions and streamline daily operations. As these tools evolve, they'll become even more crucial for long-distance warehouse management.
What's Next for Remote Warehouse Management
Remote warehouse management is evolving rapidly. Here's what's coming and how to prepare:
New Technologies
AI and automation are transforming warehouses:
1. AI-powered forecasting
AI predicts inventory needs. HQSoftware's AI platform boosts WMS performance by 40%.
2. Autonomous robots
By 2025, 4 million commercial warehouse robots will operate in 50,000+ warehouses, handling picking, packing, and transportation.
3. Drones for inventory
AI-equipped drones track inventory in real-time, creating digital warehouse twins for better oversight.
4. IoT devices
IoT enhances supply chain visibility. Aberdeen Group found IoT users saw 15% lower inventory costs and 10% more inventory turns.
5. Cloud-based WMS
These systems offer real-time data across sites, helping warehouses adapt quickly to market changes.
What Workers Want
Remote work is sticking around. Workers want:
Want | Stat |
---|---|
Remote work option | 98% of workers |
Flexible hours | 57% would switch jobs for this |
To keep your team happy:
- Offer remote options using tools like HERE Asset Tracking
- Train staff on new tech like AI and robotics
- Prioritize well-being with mental health resources
- Use tech that helps remote teams collaborate
"HERE Asset Tracking helps you know where your assets are. When working from home, you need to be more efficient. You can't waste time searching for assets with phone calls and emails." - Dobrina Laleva, Product Marketing Manager at HERE
As warehouses go digital, balance tech and human needs. Stay ahead by adopting new tools and listening to your team.
Conclusion
Remote warehouse management is evolving rapidly. New technology and changing worker needs are reshaping how we run warehouses from afar.
Here's what you need to know:
- Clear communication and daily check-ins keep teams on track
- Focus on results, not micromanaging
- AI, robots, and IoT are making warehouses smarter
- 98% of workers want remote options
To stay competitive:
1. Use AI-powered forecasting and autonomous robots
2. Offer flexible work options and mental health support
3. Implement cloud-based systems for real-time data
4. Train staff on new tech to boost skills
The key? Balance tech with your team's needs. This approach creates a remote warehouse that's both efficient and worker-friendly.